In the automotive repair and maintenance industry, the automotive repair tools and automotive equipment used in garages directly impact operational efficiency, technician safety, and customer satisfaction. For distributors and service providers, selecting the right equipment suppliers is not merely a transactional decision—it is a strategic partnership that demands trust, reliability, and adherence to global standards. This is where OEM certifications play a pivotal role. Certifications such as TÜV and ANSI act as third-party validations of quality, safety, and compliance, enabling distributors to mitigate risks and build long-term credibility.
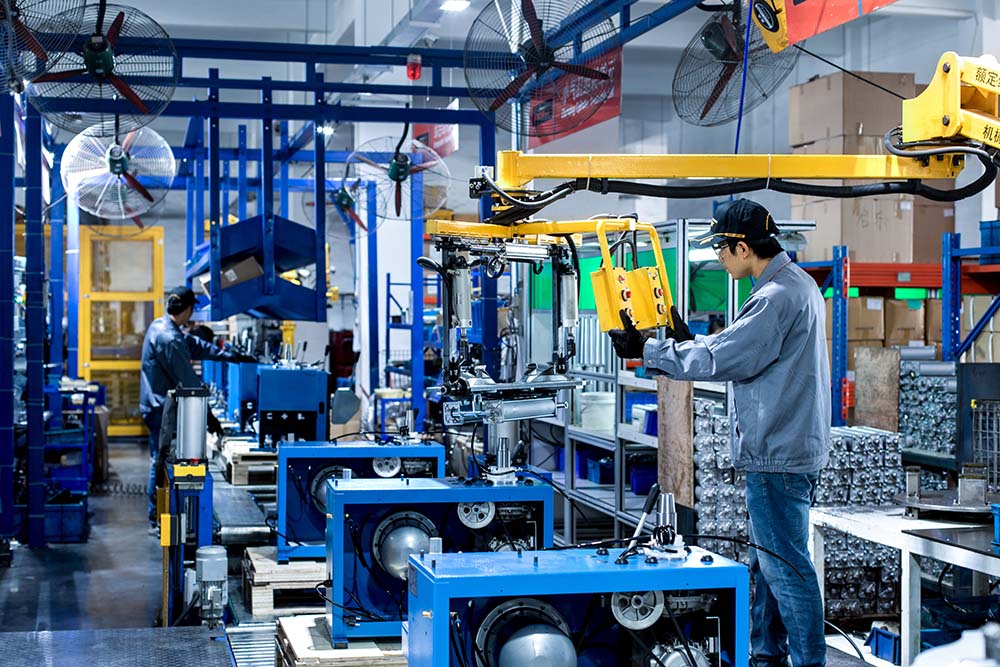
The Role of OEM Certifications in Automotive Equipment
OEM (Original Equipment Manufacturer) certifications are formal endorsements issued by independent organizations to verify that a manufacturer’s products meet rigorous technical, safety, and performance criteria. These certifications serve as a universal “language of trust,” bridging gaps between manufacturers, distributors, and end-users. Key certifications include:
- TÜV Certification
Administered by Germany’s Technischer Überwachungsverein (TÜV), this certification is synonymous with precision engineering and safety. For automotive tools like hydraulic lifts or diagnostic scanners, TÜV certification ensures compliance with EU safety directives (e.g., Machinery Directive 2006/42/EC). Manufacturers bearing this mark have undergone exhaustive testing for durability, electrical safety, and ergonomic design. - ANSI Accreditation
The American National Standards Institute (ANSI) oversees product standards in the U.S., focusing on interoperability and occupational safety. ANSI-certified garage tools, such as torque wrenches or tire changers, are validated for accuracy and alignment with industry best practices. This certification is particularly critical for distributors targeting North American markets. - ISO 9001
While not exclusive to automotive tools, ISO 9001 certification signals a manufacturer’s commitment to consistent quality management systems. Suppliers with this credential demonstrate traceability in production processes, reducing defects and ensuring scalability.
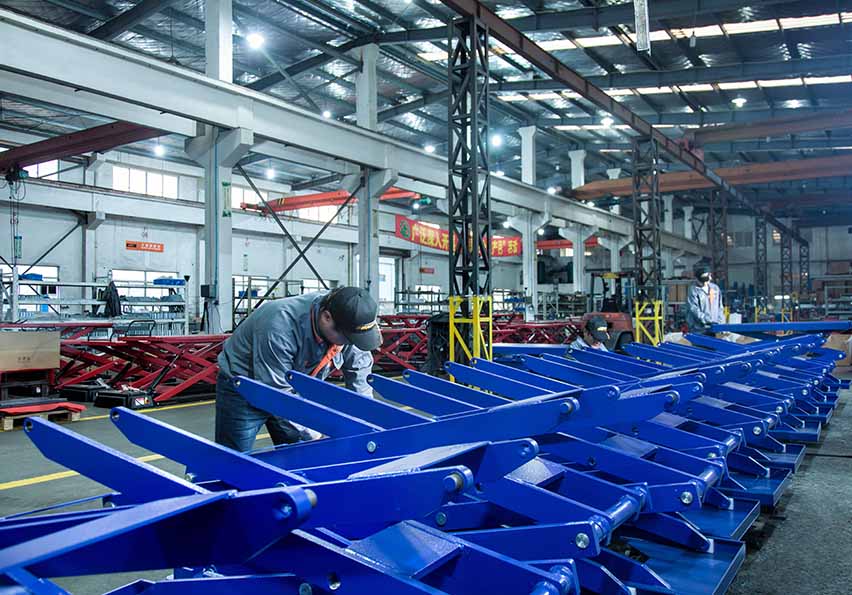
Building Trust Through Certification
For distributors, aligning with trusted equipment suppliers is a competitive advantage. Certifications simplify decision-making in three key ways:
- Risk Mitigation
Certified tools are less likely to malfunction, reducing liability risks and warranty claims. For example, a TÜV-certified car lift undergoes stress tests to handle extreme loads, minimizing the chance of workplace accidents. - Market Acceptance
End-users, such as repair shops, prioritize OEM-certified garage tools to avoid downtime and ensure compliance with insurance requirements. Distributors carrying certified products gain a reputation for reliability. - Regulatory Compliance
Certifications like ANSI help navigate regional regulations, ensuring seamless market entry. Non-compliant equipment can lead to fines or recalls, damaging distributor-manufacturer relationships.
Checklist for Evaluating Automotive Equipment Manufacturers
To identify trusted equipment suppliers, distributors should assess:
- Certification Validity
✅ Confirm active certifications (TÜV, ANSI, ISO) on the manufacturer’s website or via the certifying body’s database. - Quality Control Processes
✅ Request documentation on testing protocols, material sourcing, and defect resolution. - Compliance Track Record
✅ Investigate past recalls or non-compliance incidents. - Industry Reputation
✅ Seek testimonials from other distributors or repair facilities. - Post-Sale Support
✅ Verify warranty terms, technical support availability, and spare parts accessibility.
Conclusion
In an industry where precision and safety are non-negotiable, OEM certifications act as a cornerstone for trust. They empower distributors to differentiate themselves in crowded markets while ensuring end-users receive tools that perform as promised. By prioritizing OEM-certified garage tools and rigorously evaluating manufacturers through the lens of global standards, businesses can forge partnerships that drive operational excellence and sustained growth.
When selecting an automotive equipment manufacturer partner, remember: Certifications are not just badges—they are promises kept.